24 Jul 2020
Babcock South Africa receives energy project award for NOx abatement solution
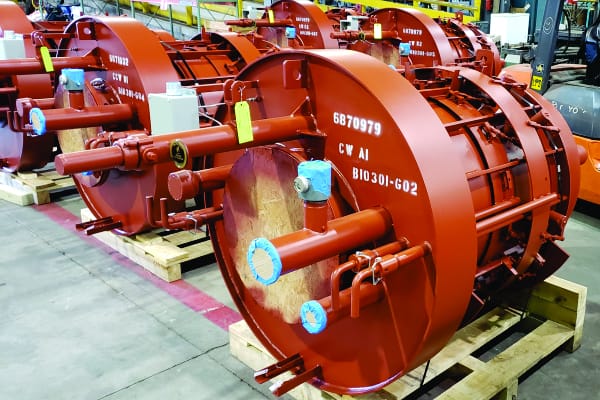
Babcock South Africa’s Ntuthuko Engineering business is leading the way in specialist combustion installations in South Africa, having successfully implemented one of the first nitrogen oxide (NOx) abatement projects in the country.
The project scope required Babcock to provide and implement an optimised NOx abatement solution for 12 boilers at a large industrial petrochemical plant, in order to comply with the National Environmental Management: Air Quality Act. The legislation calls for NOx levels to be reduced to
750 mg/Nm3 for each combustion installation with a thermal rating of more than 50 MW.
Final performance tests of the NOx abatement installation, conducted in the first quarter of 2019, indicated that NOx production was reduced to significantly lower than local environmental requirements.
The ongoing boiler plant project has been recognised for its significant contribution to South Africa’s energy environment, and has earned Babcock a South African National Energy Association (SANEA) Energy Project Award for 2019. The awards recognise projects that positively contribute to the South African energy environment or bring international credibility to the country, through leadership, innovation, initiative and vision.
Juan Gerber, Process Engineering Manager for Babcock, says that as part of the concept design phase, daily coal sample data, as well as future coal mining predictions were processed and analysed in order to establish a design coal specification.
After an extensive technology selection process, the compact Babcock & Wilcox DRB-XCL® low NOx burner was found to be the most suitable for the given site constraints, and its widespread international application demonstrated NOx reduction higher than local minimum emission requirements.
Based in the USA, Babcock & Wilcox is a global leader in energy and environmental technologies. The business has fabricated and installed over 3 000 low NOx burners locally and internationally, including 365 DRB-XCL® burners which are similar to the type used for this application.
Gerber says that through this global partnership, Babcock was able to access international expertise and adapt it to local conditions, and successfully implement global low NOx technology in an African context.
Together with Babcock & Wilcox and the customer, Babcock investigated and tested different burner configurations to establish the reaction of the low NOx burner to South Africa’s unique coal conditions. All the auxiliary boiler systems were also investigated to determine the impact to the NOx production and how they could be further optimised.
He explains that it was pivotal to match the correct technology with the project scope, which required integrating high tech burners into a 60-year old boiler plant. “Apart from its performance, the Babcock & Wilcox burner has an established installation base and proved to have minimal impact on the existing boiler plant and auxiliary equipment.”
While technology and equipment was selected to have minimal impact, parts of the existing boiler plant required modification or redesign. This included the pulverised fuel piping, main boiler structure and access platforms, pulverised coal mill plant control philosophy, boiler outlet flue gas sampling grid, fuel oil and atomising burner system, and a burner auxiliary air system. The control logic and combustion management systems were also updated.
Gerber explains that the project required integration of various engineering disciplines, together with the construction team and support staff from Babcock’s head office to develop a final solution for each of the systems involved.
He adds that Babcock took a modern engineering approach to a complex project and utilised its in-house 3D scanning and modelling capabilities to facilitate and optimise the design phase. Exacting safety standards were required taking all stakeholders into account to ensure a precise and safe outcome. Gerber adds that the 3D modelling enabled all parties, from the customer and engineers through to operators and safety officers, to review the process safely, often without requiring on-site presence.
Babcock has successfully installed and commissioned the first new low NOx Babcock & Wilcox DRB-XCL® burners into one of the boilers, and is in various stages of installation for the rest of the boilers.
Babcock’s Ntuthuko Engineering business has multidisciplinary capability comprising process, mechanical, piping, EC&I, welding and R&D disciplines, supported by project and system engineering, data management and drawing office departments. The engineering disciplines can operate individually or be combined as an engineering design group to cover simple and complex projects. All disciplines are equipped with best in class tools and the latest technologies. The engineering team has a combined experience of more than 650 years in the steam generation industry with more than 15 professionally registered engineers at ECSA, and three welding specialists registered at SAIW.