28 يونيو 2018
Cavendish Nuclear develops new technology for safer faster decommissioning
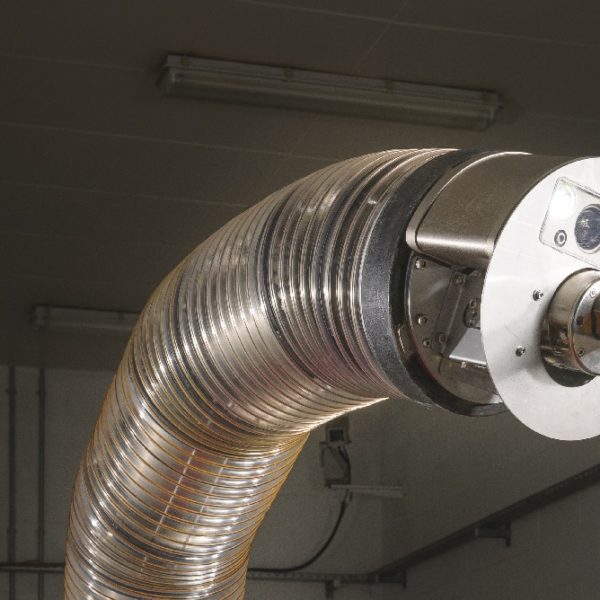
Cavendish Nuclear, working with OC Robotics and the wider Babcock International Group, is developing the next generation of world-leading robotic technology to deliver safer, faster and more cost-effective decommissioning of one of the world’s most hazardous facilities.
The company is merging its award-winning radiological mapping technology with state-of-the-art virtual reality and robotics to create a new, remotely-operated platform capable of taking apart the soon-to-be-redundant reprocessing plants at Sellafield.
The innovation in decommissioning technology is being backed by £1.5 million of R & D funding from Innovate UK, the UK’s innovation agency, including funding from the Department for Business, Energy and Industrial Strategy and the Nuclear Decommissioning Agency.
“We are combining technologies developed across different sectors of industry to deliver a breakthrough in the reduction of risks to workers, increased productivity, more efficient management of waste, reduced timescales and lower overall costs,” explained Cavendish Nuclear’s project lead Alan Rutherford.
Sellafield Ltd is seeking innovative new technology to help it decommission the site’s nuclear fuel reprocessing complex and joined forces with the UK Government, Innovate UK and the Nuclear Decommissioning Authority to create a competition for development funding.
Cavendish Nuclear, the UK’s leading nuclear services business, partnered with OC Robotics of Bristol and applied Babcock International Group’s wider virtual reality capability to come up with the Sellafield In-Cell Decommissioning System, or SIDS.
The short-listed system brings together three existing technologies – the robotic laser-snake arm of OC Robotics, the Radscan 3D gamma
dose rate scanning technology of Cavendish Nuclear, and the virtually reality expertise of Babcock– to create a remotely-operated platform that protects workers from radiation while giving them much greater visibility of the hazards.
The combination of radiation mapping and virtual reality simulation will allow operators to programme the sequence of robotic cutting in a way that synchronises with the site’s waste routes.
The system is being developed and tested at Cavendish Nuclear’s regional base at Westlakes, Cumbria, with a demonstration scheduled for late 2018.
The winning project – or projects – could be put to work at Sellafield’s Thermal Oxide Reprocessing Plant (THORP) and Magnox Reprocessing Plant, which are both due to close after fulfilling their operational roles.
Melanie Brownridge, head of technology at the Nuclear Decommissioning Authority, said: “It’s a huge challenge. The new integrated system must establish what’s inside the cells, measure the radioactivity, access spaces that have been sealed for years, cut up the contents (including large vessels and many miles of pipework), segregate the waste, then remove it for treatment and safe storage. Radioactivity levels are extremely high, restricting workforce access, so the work must be carried out remotely.
“The NDA is continually seeking the best ways to encourage innovation and bring in new ideas from the supply chain and ensure everyone has an opportunity to contribute. Part of our mission is to support innovation and technology growth, with the aim of pushing forward the decommissioning of extremely complex nuclear challenges.”
Andrew Tyrer, Challenge Director – Robotics in Extreme and Challenging Environments at UK Research and Innovation said: “Cavendish Nuclear’s deployment of robotic technology in the nuclear environment is a great example of how the UK government, via its Industrial Strategy Challenge Fund, together with other partner agencies is backing fantastic innovations with benefits for the economy and society. By developing new technologies and systems that can be deployed in these extreme environments, we can create a together a safer working world for people, as well as supporting advances in industry and public services to make them more productive.”